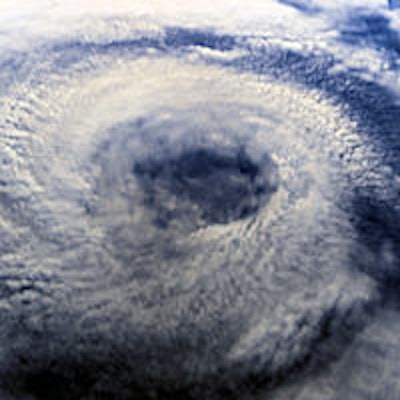
As the adage goes, "Forewarned is forearmed." With the heart of hurricane season approaching, service personnel at hospitals along the East Coast should take precautions now to ensure that natural disasters such as last year's Hurricane Sandy do not wreak havoc with their MRI scanners.
NYU Langone Medical Center in lower Manhattan was among the facilities that experienced the full force of Sandy. The center's basement and ground floor flooded, and it took two months to resume at least some diagnostic imaging and interventional radiology services at Tisch Hospital and the Schwartz Health Care Center.
"You should be prepared 12 months of the year," said Donal Teahan, director of practice development at NYU Langone. "In reality, what you prepare for in the summer is no different than what you prepare for at other times of the year. At the end of the day, you need power, chilled water, and heating, whether it is 110° outside or 10° below, whether it is a calm day or you are in hurricane season."
Power interruptions
An MRI system, for example, must be cooled to 4.2 kelvin, or -452° F, and it uses liquid helium and a chiller to sufficiently cool the magnet to that temperature. The system continues to consume power and helium to remain cool when the magnet is idling.
"Severe weather always brings the possibility of a power interruption, which is problematic for an MRI system," said John McCabe, product service director for MR in the U.S. and Canada for GE Healthcare. "Certainly, a hurricane brings the issue of duration [of a power outage] and how long will the MRI be without power. So power disruption to the electrical system is the No. 1 issue. I don't think there is a No. 2, 3, 4, or 5 issue."
Mike Witschel from Siemens Healthcare.
Even in less severe weather, power outages and fluctuations are a cause for concern for MRI systems, according to Mike Witschel, senior director of Northeast service for Siemens Healthcare.
"Oftentimes the power will go out, come back on for a while, go out again, and come back on again," Witschel said. "That is very hard on an MRI unless you have taken steps in advance to make sure that it isn't."
In addition to summer thunderstorms, periods of extreme heat can cause problems for a magnet's chiller. "In major metropolitan areas during periods of extreme heat, a utility company often may implement periods of brownouts, which can cause system or chiller malfunctions," said Sheldon Schaffer, vice president and general manager for MR/CT at Hitachi Medical Systems America. "During the transition from the heating season to cooling season and back during the spring and autumn, HVAC systems may not function correctly, causing the temperature and humidity to fluctuate outside specifications."
Optimum uptime
NYU Langone's radiology department runs from 7 a.m. to 10 p.m. on an outpatient basis seven days a week, and it conducts inpatient imaging 24 hours a day, seven days a week. The inpatient off-peak hours generally involve emergency in-house patients.
Constant preventive maintenance is one key strategy to avoid damaged equipment.
"Regular maintenance is the medicine for any problem," Teahan said. "If you maintain equipment all the time and maintain the manufacturer's specifications, in all likelihood you should never have a problem with the equipment."
Uptime is increasingly crucial when serving a patient and physician population that depends on imaging to diagnose maladies and also to maintain a certain level of revenue due to declining cuts in reimbursement. Therefore, some facilities may not take the time to perform preventive maintenance, opting instead to keep MRI systems and other imaging technology running as much as possible.
However, those circumstances are all the more reason to perform regular checkups, Teahan said. "We have to provide the best service possible to all patients; the only way we can do that is to be up and running and available when they need us," he added. "There is no value in offering someone an MRI at 4 o'clock in the morning unless they are already in the hospital and need it. For those situations, we have secondary equipment."
To that end, Teahan observed that vendors have developed stronger partnerships with imaging facilities and understand the need to preserve peak imaging time.
"I look for contracts now for preventive maintenance, upgrades, and service at 4 o'clock in the morning, when we will affect neither patients nor my ability to run the department," he said.
During periods when temperature and humidity in the scanning environment are stable and the chiller is working correctly, systems typically do not experience many issues if they are being properly maintained by the manufacturer, added Hitachi's Schaffer. Thus, customers should ensure that their chillers and HVAC systems are receiving adequate scheduled maintenance so that they remain in top condition.
Post-Sandy reflection
Siemens used the experience of Hurricane Sandy to reflect on what happened and what could have been done differently to limit the impact of adverse events. Related power outages, for example, can destroy MRI components or weaken them so the component soon fails.
"In either case, it's not good because it results in downtime," Witschel said.
Siemens developed a process for customers to secure their MRI systems in advance of a predicted storm by designating a staff person to be trained on issues such as when to power down an MRI magnet.
"What we would like to see happen is that the system be taken through a 'power down' and allow the storm to pass," Witschel said. "That would prevent fluctuations that can happen when power comes back on temporarily. When that happens, you get in-rush current, then it goes away, and that is the kind of thing components don't like."
There are, of course, ramifications for powering down an MRI scanner, as it takes time to bring the device back online and results in downtime. Helium consumption also will increase to keep the magnet cool.
Remote monitoring
GE, Siemens, and Hitachi have the ability to monitor a customer's MRI scanner remotely to keep tabs on the system's status. With GE's technology, the device "will make a decision whether to casually supply data because it is programmed to do so on an interval, or whether to urgently push data because a particular parameter may soon be out of specification," McCabe said.
John McCabe from GE Healthcare.
The generation of status reports can be timed according to circumstances such as an approaching hurricane.
"We can set these monitors to call in as often as once per minute," he added. "If everything is running normally, our devices generally check in at least once per day."
In the case of Hurricane Sandy, GE had some 250 magnets along the East Coast, which needed monitoring at will. The company could query the systems to see how a scanner was performing rather than wait for a report to be sent.
To track Hurricane Sandy, GE superimposed the National Weather Service's projected path of the storm over a map of the locations of the company's MRI systems. "All of the MRI systems that would be affected [by the hurricane] lit right up," McCabe said.
Hitachi includes chiller maintenance in its warranty and full-service contract coverage to ensure systems are well-maintained. Customer systems that are under warranty or a service contract are also monitored by Hitachi's remote service monitoring system so that appropriate action can be initiated when problems arise.
Recently, a Hitachi customer in Oklahoma experienced a direct lightning strike to its chiller during a tornado. Hitachi arranged for a replacement chiller to be shipped from the manufacturer over a weekend to protect the system from catastrophic helium loss and to get it back in operation quickly. The response prevented the customer from losing all of the helium and having to restart the magnet.
Better communication
The best advice Teahan offered is to listen to the technicians handling the equipment to find out how well the technology is running. "They spend more time with the equipment than the vendors, support people, or anyone else," he said.
To bolster communication, NYU Langone invites its service managers and engineers, vendors, and technical staff to the facility for lunch every quarter. "I know this sounds corny, but people work better with one another when they know one another," Teahan said. "It's nice when they sit down and have lunch and they are not under stress or a timeline."
If there are any issues during the quarter, those concerns are discussed. Teahan said it is often a case of miscommunication and the meeting ends with a better understanding of the situation.
"Train your staff and treat your vendors properly, and they will always come back to support you," he said. "You can't predict issues, but you can make it so that you get the best support available."