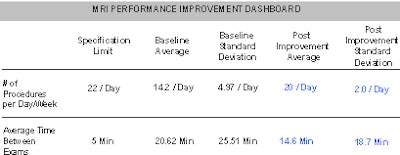
In today’s competitive environment for outpatient imaging services, it is imperative to be as resourceful as possible. Declining reimbursements, increasing costs, and competition from entrepreneurial physician groups make operational efficiencies a must-have for hospital-based imaging centers. One approach that is proven to effectively increase efficiency is Six Sigma -- a didactic statistical methodology for improving and reducing the amount of variation in any process.
The most frequently used model in Six Sigma is based on the DMAIC approach: define, measure, analyze, improve, and control. While this article is not meant to provide a detailed explanation of the many statistical tools that can be used -- or a comprehensive analysis of normal versus discrete data -- it does offer an overview of a practical application for the Six Sigma DMAIC approach within diagnostic imaging.
A high-level process map of an imaging patient encounter is shown in figure 1, and Six Sigma methodologies can be used to improve each of the sub-processes along this continuum. For this article, we will concentrate on the patient throughput process.
![]() |
Figure 1, image courtesy of James Yanci, GE Medical Systems. |
In terms of efficiency, capacity, and speed, having the latest technology with faster capabilities is only part of the solution. Radiology managers often feel that by adding newer, faster technology that it will reduce backlog and increase the number of patients per day. Another common belief is that throughput could be expedited if only more staff could be added to help with tasks such as patient prep.
However, even though adding staff and technology may help increase overall numbers by adding capacity, it is not always the most economical way to become more efficient. More often than not, if a Six Sigma approach is appropriately applied, patient throughput and procedures per day will increase utilizing the same staff.
As an added benefit, Six Sigma empowers employees by allowing their input into the problem areas and voicing potential solutions. This activity also assists in making improvements last by changing the way the organization works.
![]() |
![]() |
![]() |
![]() |
Figure 2, image courtesy of James Yanci, GE Medical Systems. |
Going through each phase of the DMAIC process, as illustrated in figure 2, can statistically illustrate improvement in patient throughput. However, it may also illustrate that the process improvements were perhaps based on luck or coincidence.
With Six Sigma, there is significant statistical rigor one strives for to achieve an increase in process improvement. Thus, utilizing this methodology may not at first demonstrate an improvement, and other steps in the measure and analyze phases may need to take place if the correct factors are not identified the first time.
During the initial "define" phase, the team will select and scope the project, setting parameters that are manageable and measurable. In our example, we defined our objective to grow revenue by expanding capacity and patient throughput.
Measuring the process is a stringently controlled step that is defined in detail. One such example would include analyzing the measuring tool to see if it is adequate and not flawed when collecting data.
As an example, a RIS works well because it is an automated methodology. When using manual methods of data collection, however, it is imperative to train all staff on how to collect and interpret the data definitions.
Once the baseline data is collected, it can be synthesized into calculating current state average times and standard deviation of the process. See figure 3, below, for sample results of our fictitious hospital.
![]() |
Figure 3, image courtesy of James Yanci, GE Medical Systems. |
A key step in the analysis is to set performance standards. Before analyzing the data, a target value and upper or lower specification limits are set to identify where you want to be in each cycle.
The example in figure 3 illustrates that time between exams has the highest variability. The defined upper specification limit is 5 minutes, with a target of 3 minutes. As illustrated, 20.62 minutes is well above the upper specification limit of 5 minutes. This process clearly indicates the greatest opportunity for improvement.
![]() |
Figure 4, image courtesy of James Yanci, GE Medical Systems. |
Now for the fun part of a Six Sigma project: improving. A tool known as workout can be used effectively during this phase. Workout is a process whereby the key stakeholders involved convene to brainstorm and categorize potential causes, prioritize potential solutions, and develop action plans to implement changes.
The key to this session is to involve the person who has the authority to make changes happen. Items for our hospital include things such as improving patient transport, educating physicians on certain types of protocols, and having transporters assist in preparing patients when not busy.
After the changes have been implemented, a remeasuring phase takes place. Using tools such as the two-sample t test can determine if a statistically significant change has been made.
Following through with the example shown in figure 3, not only did time between exams decrease, the change allowed for the total number of procedures to increase from an average of 14.2 per day to 20 per day, post improvement.
Once it has been determined that a statistically significant improvement was made, a plan is developed to make sure that the change will be sustained and monitored, or controlled. Some of the ways this can be accomplished include implementing new standard operating procedures and creating a quality plan.
With the project in the control phase, you can create a business case by looking at new potential revenue that can be generated through increased procedure volume and less variation in operational processes.
Keep in mind that even if a backlog does not exist, it is important to know that the department is operating as efficiently as possible. Other areas that may be suitable as Six Sigma projects -- such as staffing and supply costs -- can be identified during the improvement process and may yield additional benefits.
Having the capability to financially impact your business with significant, documented results that can be shared with senior management is always a prudent goal. Achieving productivity performance improvement utilizing the rigor of Six Sigma is the vehicle that can get you there.
Remember:
- Define the problem.
- Measure with correct tools.
- Analyze the data and identify areas to improve.
- Improve by identifying potential solutions to the problem and implement changes.
- Control your improvements using dashboards and standard operating procedures.
By James Yanci
AuntMinnie.com contributing writer
January 2, 2004
James Yanci is a senior consultant and Six Sigma Black Belt with the Performance Solutions group at GE Medical Systems. His background includes more than 16 years of healthcare experience in areas such as medical equipment sales management, strategic marketing, business plan development, market analysis, project management, management information systems, clinical laboratory aptitude, and GPO contract management.
Related Reading
Workflow analysis can ease scheduling woes, November 28, 2003
Imaging centers ready to handle cost-conscious market, April 3, 2003
Billing blues: Eliminating denials for imaging services, March 13, 2003
Computerized order entry yields benefits, February 7, 2003
Go with the flow: Is your facility designed for maximum utilization?, November 18, 2002
Copyright © 2004 GE Medical Systems