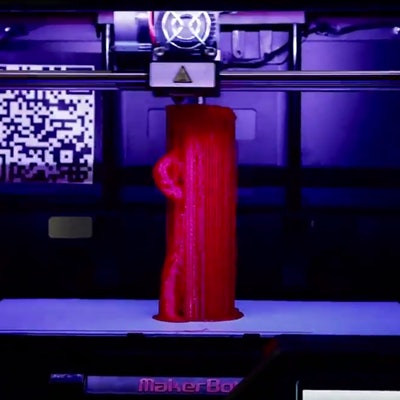
The good news is that humans are living longer. The bad news is that our bodies are wearing out as we age, creating the need for replacement parts that are customized to individual patients. A center in Arizona is doing just that, developing 3D printing techniques to keep people healthy and active into their old age.
At the University of Arizona in Tucson, researchers are pushing the envelope in 3D printing, creating surgical models, operating room tools, and even first attempts at replacement organs. They have developed intraoperative templates to guide reconstruction tasks throughout the body and particularly in head and neck surgery, where complex anatomic structures require extensive familiarity with the subject before attempting surgery.
Body parts on demand
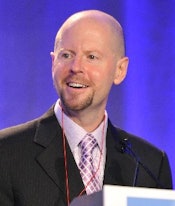
It was the prospect of the just-in-time creation of models for surgeons that sparked the interest of Dr. David Armstrong, PhD, a professor of surgery and director of the Southern Arizona Limb Salvage Alliance (SALSA) at the university.
Armstrong, who was recently profiled in an article in the Lancet (October 1, 2016, Vol. 388:10052, p. 1368), got his start in 3D printing several years ago with a consumer-grade fused deposition printer, which the group used to print Army-Navy surgical retractors. These turned out to be sterile and strong enough for use in the operating room -- and definitely cheap enough at 46¢ apiece. Since then, the group has moved on to create surgical models of all kinds
"For the past several years, we've been among the first to publish templates for plastic surgery and head and neck reconstruction," Armstrong told AuntMinnie.com.
The better to hear
In 2015, researchers with the center published a paper on using 3D-printed templates for ear reconstruction in children with microtia, a congenital deformity of the pinna that can lead to poor development of the ear.
Creating a template for surgical reconstruction is fairly straightforward, Armstrong said. The group uses an application called 123D catch (Autodesk) to manipulate an image of an ear, much the way Photoshop would be used. The image is then sent to a 3D printer for production.
The precise ear template can be used in the operating room to assist the surgeon in carving out bone cartilage and skin from the patient to create the ear, he said.
"You can take a rib from the young man or the young woman -- this seems almost Biblical -- and then you can actually reconstruct an ear with some skin from the patient and create a new ear," he said.
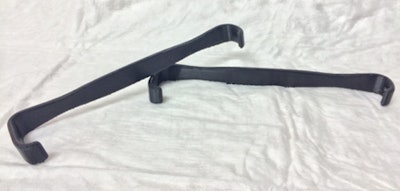
Proving remote printing
Armstrong and colleagues, along with a group from the University of California, San Diego, also pioneered the use of remote 3D printing, a process by which printing instructions are sent to a remote 3D printer, avoiding the need to be where the final product is printed.
"We thought it would be cool if you could send a low-cost printer to far-flung place, and then, instead of building all this instrumentation and having to deal with import-export stuff, we could just print a few things there."
Surgical instruments -- or really anything that's in short supply where the patient is -- could theoretically be printed onsite, even in remote locations like Antarctica. Armstrong acknowledged the thorny intellectual property issues that can come with replicating tools "just like ripping a CD."
"It's all going to have to be sorted out, but we published on our passion of creating basic and not-so-basic surgical instrumentation," he said.
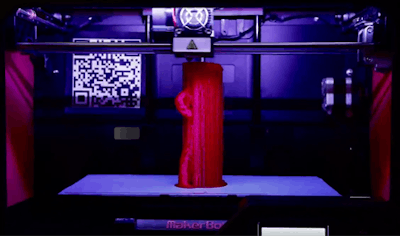
Complex body parts
The group has been doing complex reconstruction for a number of years now "to where we can print out the musculoskeletal template to give us a real plan of reconstruction," Armstrong said.
"It may not look complicated, but it's extraordinarily complicated in terms of musculoskeletal anatomy, especially something like the head and neck," he said.
One can also print out soft-tissue structures in the mediastinum to facilitate planning for reconstruction or resection. The creation of complex models has progressed far beyond games or proof of concept -- it is done fairly quickly and quite regularly at the university, according to Armstrong.
Just the beginning
Beyond educational models, researchers in Boston are working on customized implants and even functional models, printing vital structures as the first step in creating working 3D-printed organs, Armstrong said.
"They have begun the process of what's called composite 3D printing, where you can deposit different kinds of substances and make either a template or, ultimately, a body part," Armstrong said.
Researchers from the Harvard John A. Paulson School of Engineering and Applied Sciences are using customized multimaterial bioprinters to approach their goal of printing vascularized tissues and eventually organs, according to the Lancet article, which also featured Jennifer Lewis, ScD, a professor at Paulson.
The tissues printed in Lewis' lab contain embedded tubular channels that serve as vascular architecture and can be lined with endothelial or epithelial cells. This enables the printed models to mimic vasculature or kidney proximal tubules, offering hope of eventually creating new organs and perhaps even cutting down on the wait list for transplants.
"This stuff is starting to take on a pretty cool reality," Armstrong said of the work.
Replacing worn-out parts
"What's happening now as a species is that fewer and fewer of us are dying from infectious diseases, even though there are still far too many of them out there," he said. "But for the first time now we're dying more from noncommunicable diseases -- things like diabetes, cancer, and cardiovascular disease. And we have to figure out a way to delay decay in some way. How do we do that? Replacement parts, and that's where this stuff might play a role."