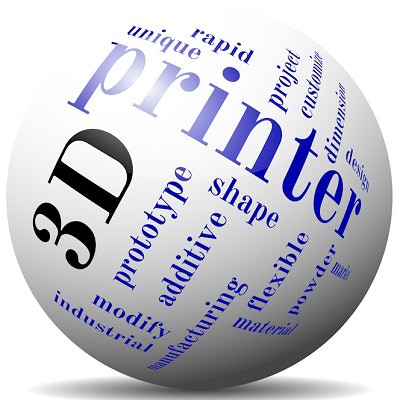
How might 3D-printed knee jigs help improve the quality of total knee replacement surgery? Researchers from India discussed the benefits of using these patient-specific models for the task in a review article published in the most recent issue of the Journal of Clinical Orthopaedics and Trauma.
Total knee replacement is a challenging procedure that is subject to a wide range of complications, including intraoperative fracture, as well as poor long-term patient outcomes. Recently, various groups have attempted to improve outcomes by incorporating patient-specific 3D-printed models into the process, not only for presurgical planning but also to guide implantation intraoperatively as well, noted first author Dr. Raju Vaishya and colleagues from Indraprastha Apollo Hospital in New Delhi.
In the case of 3D-printed knee jigs, clinicians have used these patient-specific models during knee replacement surgery to determine precisely what parts of the knee bones they need to cut before finally attaching the prosthesis. Building such 3D-printed models roughly entails acquiring CT scans of the patient's knee, designing 3D virtual models based on these images, and then printing the models with a 3D printer and biocompatible materials (J Clin Orthop Trauma, July-September 2018, Vol. 9:3, pp. 254-259).
To evaluate the benefits of using 3D-printed knee jigs for knee replacement, the group searched for relevant clinical studies and found that the technique offered several advantages over conventional and computer navigation-assisted techniques:
- Identifying surgical cuts. Traditionally, orthopedic surgeons have made cuts on the femur based on a fixed femoral valgus angle, the measured angle between the length of the bone and an imaginary line connecting the hip joint to the knee. Yet there is considerable variability in the size of this angle among different patients that traditional methods do not take into account. In contrast, patient-specific 3D-printed jigs provide clinicians with a more exact angle measurement and, thus, better predict the ideal spot to cut the bone, according to the authors.
- Estimating implant size. 3D-printed jigs also enable the surgical team to determine preoperatively the size of the implant required for each patient with high accuracy, whereas conventional techniques often fail to do so, Vaishya and colleagues noted. Having this knowledge beforehand may help decrease the cost of transporting and storing multiple implants of different sizes, as well as reduce the duration of surgery.
- Improving knee bone alignment. Examining 3D virtual models of the patient's knee before the operation gives surgeons the chance to decide exactly how they will align the femur and tibia, potentially improving postoperative limb alignment.
Furthermore, recent technological advancements in medical 3D printing have helped lower costs and shorten production times -- two major barriers to using 3D-printed knee jigs. It takes less than a week and under $400 to make and deliver a model.
"3D-printed patient-specific jigs can be used for prediction of component sizes in total knee replacement, which can help in improving [operating room] efficiency and decreased armamentarium. ... Their usage is still in its early stage and more studies with a larger number of patients and longer follow-up will help in establishing their role in total knee replacement," the authors wrote.